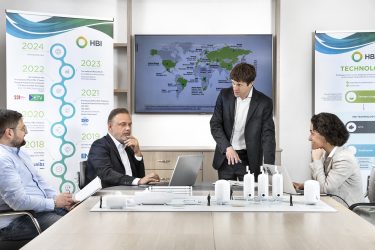
L'energia del futuro dai fanghi di depurazione: intervista a Daniele Basso di HBI Group
Attualmente in Europa si producono 50 milioni di tonnellate di fanghi di depurazione all’anno, mentre nel mondo 200 milioni. Secondo l’ISPRA, ad ogni italiano corrispondono circa 20 kg di fanghi all’anno e il trend prevede un costante aumento negli anni a venire.
È in questo contesto che interviene HBI (Human Bio Innovation) Group, l’azienda fondata nel 2016 da Daniele Basso, ingegnere ambientale, e Renato Pavanetto, imprenditore. Un incontro che ha trasformato le buone intenzioni in azioni concrete nei confronti dell’ambiente. HBI infatti, ha ideato, sviluppato e brevettato un sistema per il trattamento dei fanghi industriali, dei fanghi da conceria e dei rifiuti biodegradabili in grado di recuperare l’85% dell’acqua contenuta al loro interno e produrre energia rinnovabile. Il tutto riducendo di oltre il 90% il materiale altrimenti destinato a discarica o incenerimento.
Abbiamo intervistato Daniele Basso, CEO di HBI, che ci ha spiegato come funziona l’impianto e quali vantaggi porta per i gestori dei cicli idrici e per l’ambiente in generale.
Daniele, partiamo dal principio. Quale è la mission di HBI?
HBI nasce a Treviso nell’ottobre del 2016 dal desiderio di implementare i risultati del mio dottorato. In questi anni, la fase di ricerca, sviluppo e business development dei nostri progetti è stata portata avanti a Bolzano, precisamente al NOI Techpark, in collaborazione con UniBz, mentre la parte di progettazione, ingegneria e prototipazione ha continuato ad avere base a Quinto di Treviso con CARRETTA Srl, partner tecnico per la robotica e le automazioni industriali. L’idea alla base consiste nel voler sviluppare soluzioni per l’industriaattraverso attività di ricerca, prototipazione e dimostrazione di tecnologie innovative. Tra queste, quella relativa ai fanghi di depurazione.
Da quale esigenza è nata questa tecnologia?
Il paradigma di partenza è stato quello di vedere i fanghi come una risorsa al cui interno si trovano acqua, energia e nutrienti, piuttosto che come scarto. Attualmente, infatti, i nutrienti che utilizziamo in agricoltura provengono da Paesi extra UE: in questo modo alimentiamo un’economia lineare che non è soltanto svantaggiosa in termini di costi, ma è anche poco sostenibile. Ci è sembrato quindi necessario intervenire in questa direzione e trovare una soluzione innovativa che evitasse di mandare in discarica i fanghi e, con loro, le preziose risorse che contengono.
Come funziona questo processo di trattamento dei fanghi di depurazione?
Il trattamento avviene tramite più fasi. Nella prima si separa chimicamente e si recupera circa l’85% dell’acqua presente all’interno dei fanghi e si ottiene un materiale ad alta densità energetica, chiamato hydrochar. Successivamente questo materiale entra nel secondo step e viene trasformato in syngas, un gas utilizzato per alimentare la caldaia e rendere quindi la macchina neutrale. Inoltre, in questo passaggio si ottiene anche un ulteriore materiale solido, più precisamente una polvere, all’interno della quale si trovano i nutrienti riutilizzabili in agricoltura. In questo modo, la nostra tecnologia consente di separare – e quindi recuperare – dai fanghi di depurazione materiali ad alto valore aggiunto. La natura autotermica dei processi, combinata con la possibilità di produrre energia rinnovabile, consente al sistema di essere totalmente autosufficiente dal punto di vista energetico. Inoltre, abbiamo sviluppato e brevettato un dispositivo mediante il quale il sistema integrato risulta essere completamente privo di emissioni gassose ed odorigene. Attualmente ci stiamo concentrando sull’estrazione di ammoniaca e macronutrienti, anche se potenzialmente in futuro saremo in grado di separare ed estrarre anche altri materiali, a tutti gli effetti rinnovabili totalmente sostenibili e a zero emissioni.
Questa estate avete raggiunto un traguardo importante, il quarto brevetto italiano. Attraverso quali migliorie all’impianto l’avete ottenuto?
Gli ingegneri e i ricercatori di HBI hanno ottimizzato il design complessivo dell’impianto, mettendo a punto un sistema di controllo dell’intero processo cui sono sottoposti i fanghi che consente di ottimizzarne l’efficienza e migliorare il recupero termico complessivo. Ma c’è un altro risultato importante.
Il contesto normativo italiano in merito è vetusto, e considera incenerimento qualsiasi tecnologia innovativa che implementi processi chimici a un rifiuto, sia esso fango o un altro tipo di scarto. Il lavoro più grosso che abbiamo dovuto fare, quindi, è stato quello di proporre un’interpretazione normativa differente, per dimostrare – sulla base di risultati concreti – che la nostra tecnologia non è associabile all’incenerimento. Fortunatamente siamo riusciti in questa impresa, facendo in modo che i nostri impianti di trattamento dei fanghi di depurazione fossero autorizzati come “trattamento fisico-chimico”, in quanto il gas prodotto è purificato in misura tale da non costituire più rifiuto e le sue emissioni non sono superiori a quelle derivanti dalla combustione del gas naturale.
Quali vantaggi porta l’impianto per i gestori dei cicli idrici? E come si riflette ciò a livello nazionale?
L’utilizzo del nostro impianto porta numerosi vantaggi per i gestori dei depuratori delle acque reflue; tra tutti, direi che il principale è la netta riduzione dei costi di gestione dei fanghi senza dover ricorrere a nuovi investimenti in conto capitale. Proiettata a livello nazionale, tale riduzione si traduce in un potenziale risparmio per il sistema produttivo, per gli enti locali e per la collettività, che va tra i 120 e i 150 milioni di euro su base annua. Anche da un punto di vista ambientale i vantaggi sono molti: come già spiegato infatti, l’impianto consente di estrarre acqua pulita, produrre di energia rinnovabile, recuperare materiali ad alto valore aggiunto quali ammoniaca, fosforo ed altri macro e micro nutrienti utilizzati in agricoltura, ridurre gli scarti finali del 90%e infine sterilizzare i materiali residui, così da eliminarne completamente la carica batterica.
Dove è stato installato l’impianto e quali sono gli esiti?
La prima macchina a scala preindustriale è stata installata per sei mesi nel depuratore di Bolzano, attraverso il supporto di una legge provinciale. Successivamente, la macchina è stata trasferita a presso il sito GPLab di Veritas a Fusina (VE), dove sono state condotte una serie di campagne sperimentali. In totale, questa tecnologia ha superato le 8.000 ore di funzionamento, trattando circa 800 tonnellate di fanghi e raggiungendo tutti i risultati di processo prestabiliti. Si è trattato di una vera e propria fase di ricerca, che abbiamo portato avanti anche grazie al team del professor Marco Baratieri di UniBz e a Stefano Dal Savio, responsabile Tech Transfer Green al NOI Techpark. Sulla base dei risultati ottenuti, nel novembre del 2022 la nostra tecnologia ha ottenuto da Rina una certificazione ETV – Environmental Technology Verification.
Quali sono i programmi per i prossimi mesi?
In programma c’è la realizzazione di due impianti industriali in Italia, che ci consentiranno di completare l’industrializzazione della macchina. Di conseguenza, il 2024 ci vedrà impegnati nell’ingresso in maniera più strutturata nel mercato.
Vittoria Battaiola
Immagine in apertura: foto di HBI Group